COMPANY
Company Specializing in Solutions for Cellular Concrete Production
We are a company specializing in the production of additives and machinery for cellular concrete manufacturing. For over 40 years, we have provided advanced and customized technological solutions for the construction industry, supporting installers, contractors, designers, block producers, and prefabricators worldwide.
Our History
Isoltech was one of the first Italian companies to introduce systems for producing cellular concrete using specialized machines and foaming agents. Thanks to our specialized expertise, acquired over decades of experience, we have carved out a significant role at the international level. We offer not only high-quality products but also continuous support and long-term collaboration with our clients, ensuring they always achieve the best results.
CELLULAR CONCRETE
Three key elements guarantee excellence in cellular concrete production:
Quello che abbiamo riscontrato in anni di esperienza diretta sul campo e che cerchiamo di trasferire ai nostri clienti per produrre cemento cellulare di buona qualità è il necessario connubio di tre fattori fondamentali:
Innovative Technology
We use state-of-the-art machinery and foaming agents designed to deliver superior performance.
Specialized Experience
Our team of experts is always available to provide technical advice and qualified support.
Tailored Customer Support
We provide customized solutions for every need, guiding our clients through every stage of the production process.
IL METODO
A Know-How Company Serving Clients: Our Approach
Our activity goes beyond selling foaming agents, machinery, and turnkey plants.
We offer an integrated and highly personalized service, providing our clients with all the tools and expertise needed to autonomously produce cellular concrete.
Supplying machinery is just the beginning of a relationship based on collaboration and continuous support.
Our working method develops through several phases:
PRELIMINARY TESTING OF RAW MATERIALS
In our in-house laboratory, we test raw materials sent by the client, which are easily sourced from the target market, to conduct a feasibility study.
CUSTOMIZED SOLUTIONS
Following the raw material test, we optimize the formula based on the client's specific needs and the required applications.
TRAINING AND ON-SITE STARTUP
We train plant personnel at our facility. Subsequently, we assist the client on-site for the plant startup alongside our technicians. The presence of Isoltech personnel is crucial to the successful startup and initial production of cellular concrete.
CERTIFICATION OF CELLULAR CONCRETE PROPERTIES
We provide our certifications and assist the client in obtaining their own.
SPECIFIC PRE/POST-SALES CONSULTING
We offer pre/post-sales assistance and commercial presence at local events and trade shows.
CERTIFICAZIONI DELLE PROPRIETÀ DEL CEMENTO CELLULARE
Nel nostro laboratorio interno testiamo le materie prime, inviateci dal cliente e facilmente reperibili nel mercato di riferimento, per eseguire uno studio di fattibilità.
Today, Isoltech continues to innovate and improve its cellular concrete solutions,
reaffirming its leadership role in the industry.
SUSTAINABILITY
Corporate Sustainability: Our Path to Certification
CERTIFICATIONS
Company Certifications
Continuous commitment to quality, safety, and sustainability.
ISO 9001: QUALITY
MANAGEMENT CERTIFICATION
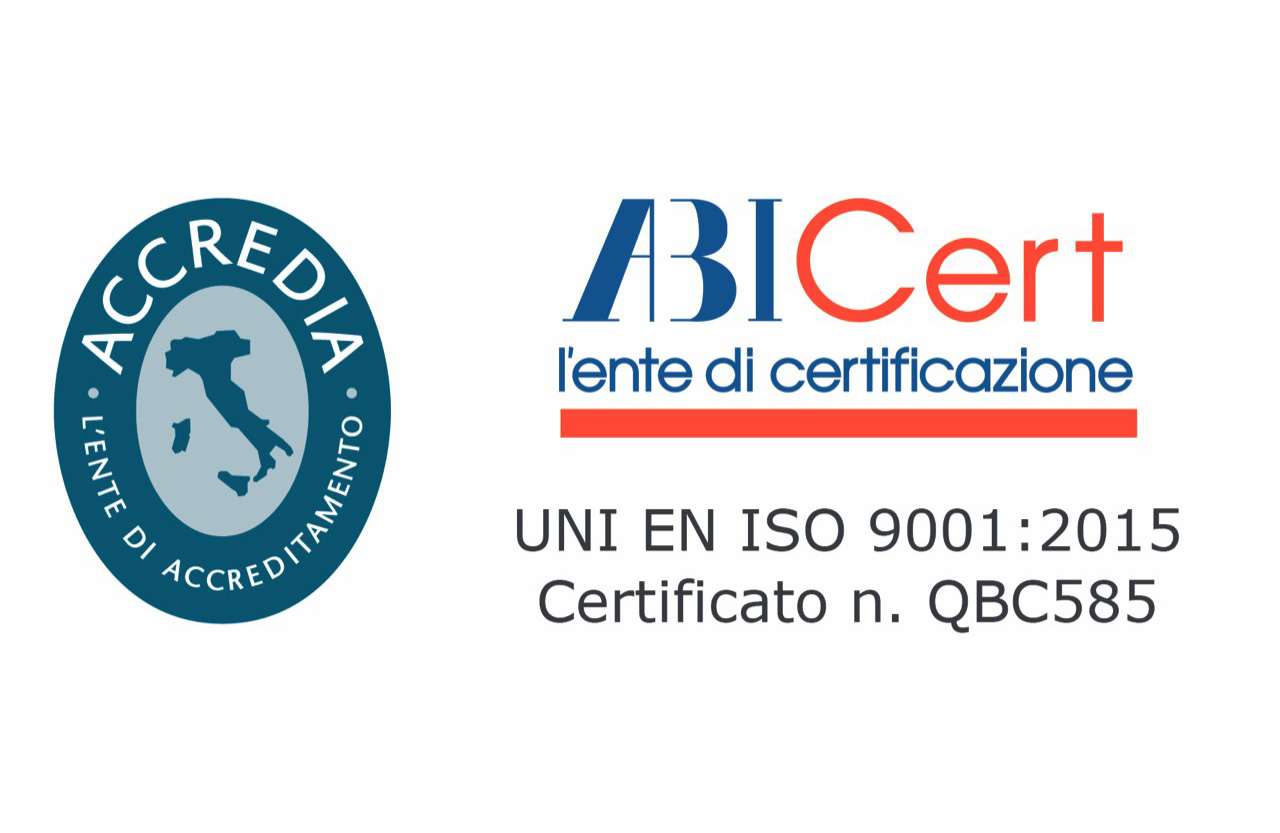
ISO 14064-1: CARBON
FOOTPRINT CERTIFICATION
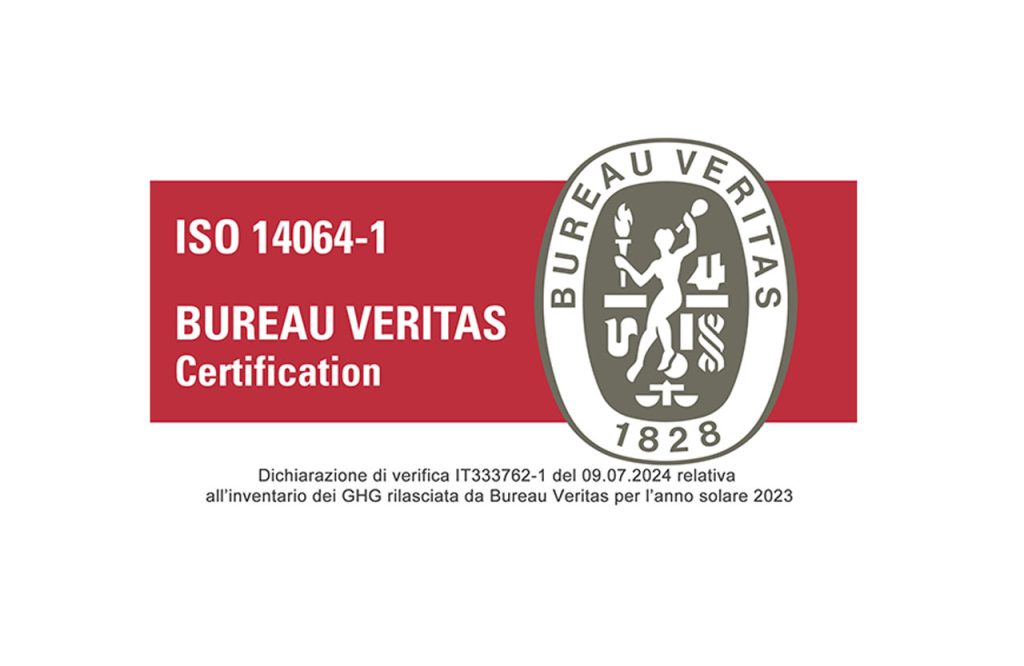
Product Certifications
Reliability and guaranteed performance for excellent results
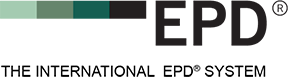
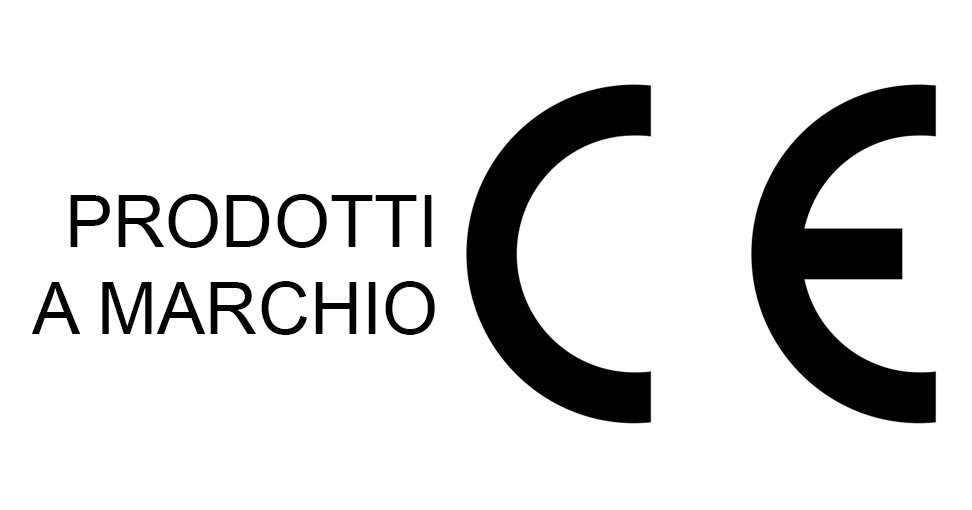
ASTM C-869
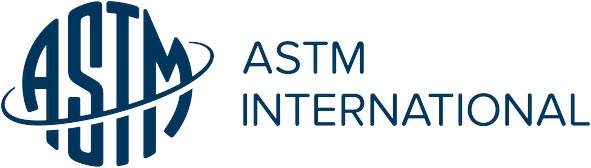
Produci Schiuma Minerale
Isoltech ha realizzato e brevettato una tecnologia costruttiva a basso impatto ambientale, capace di sostituire materiali ben più conosciuti, ma meno efficaci garantendo inoltre un elevato potere isolante. Questa tecnologia, fiore all’occhiello della conoscenza di Isoltech, consente di produrre schiuma minerale con densità comprese tra 100 e 200 kg/m3.
Brevetti
BREVETTI E TECNOLOGIA ECO-COMPATIBILE
Isoltech è attenta alla salvaguardia del pianeta e da anni si prodiga nell’individuare soluzioni tecnologiche innovative che hanno come obiettivo il riutilizzo in campo edile dei rifiuti industriali.
La tecnologia Hi-Tech Isocem S/X, brevettata di recente, si basa sul concetto di usare solo rifiuti o materie prime seconde, a base silicea: fly ash (fumi da centrale termoelettrica), silica fume (da forni elettrici di leghe di ferro-silicio), vetro macinato, silicio (da recupero di pannelli fotovoltaici), cenere di canna da zucchero, cenere di pula di riso.
Di recente si è potuta sperimentare ed utilizzare la “marmettola” (polvere di marmo) proveniente da cave di marmo, come scarto del taglio.
In questo modo si compie un circolo virtuoso che ricicla materiali di scarto generando un importante risparmio energetico sia nella produzione del cemento cellulare che nel suo isolamento termico.
Attestati
ATTESTATI & RICONOSCIMENTI
Isoltech è una azienda certificata ISO 9001 e socia di Conpaviper, a dimostrazione del suo continuo interesse per le tematiche del settore di riferimento.
Il nostro continuo sforzo in ambito di ricerca e di sviluppo è stato riconosciuto anche dalla Camera di Commercio di Bergamo, la quale nel 2010 ci ha insigniti del Premio per l’Innovazione Tecnologica.
TEAM
Discover our team
Expertise, leadership, and global vision: meet the team leading our company into the future.